Thermal oil boilers are used to reach high temperatures at low pressure.
The chemical, textile, power and process industries need heat transfer with a high
temperature fluid. The most ideal solution for such process steam requirement is
smoke tube boilers.
To reach these high temperatures, thermal heat transfer oils are used, which still remain in the liquid phase at these temperatures. The most important issue to be considered in order for organic and synthetic thermal oils to last for many years without deterioration is the thermal oil film temperature.
Therefore, thermal oil boiler construction is made coil type spiral liquid tube. This spiral structure also forms the combustion furnace.
As MNK, the connection between the 1st pass and the 2nd pass is designed as wet. Thus, refractory is not used in the rear reversal cell.
For extremely high temperature vapour thermal oil system is using.
To reach these high temperatures, thermal heat transfer oils are used, which still remain in the liquid phase at these temperatures. The most important issue to be considered in order for organic and synthetic thermal oils to last for many years without deterioration is the thermal oil film temperature.
Therefore, thermal oil boiler construction is made coil type spiral liquid tube. This spiral structure also forms the combustion furnace.
As MNK, the connection between the 1st pass and the 2nd pass is designed as wet. Thus, refractory is not used in the rear reversal cell.
For extremely high temperature vapour thermal oil system is using.
Key Features
Thermal Oil | Fuel Types | Capacity | Pressure | Efficiency | Design Life | Emission | Temperature |
---|---|---|---|---|---|---|---|
Liquid and Vapour* | Gas, Oil, Hydrogen | up to 24 MWt | up to 30 barg | up to 105%** | 30 years | <20 mg/kW | up to 400°C |
**) based on
Emission
*)with vapour
Efficiency
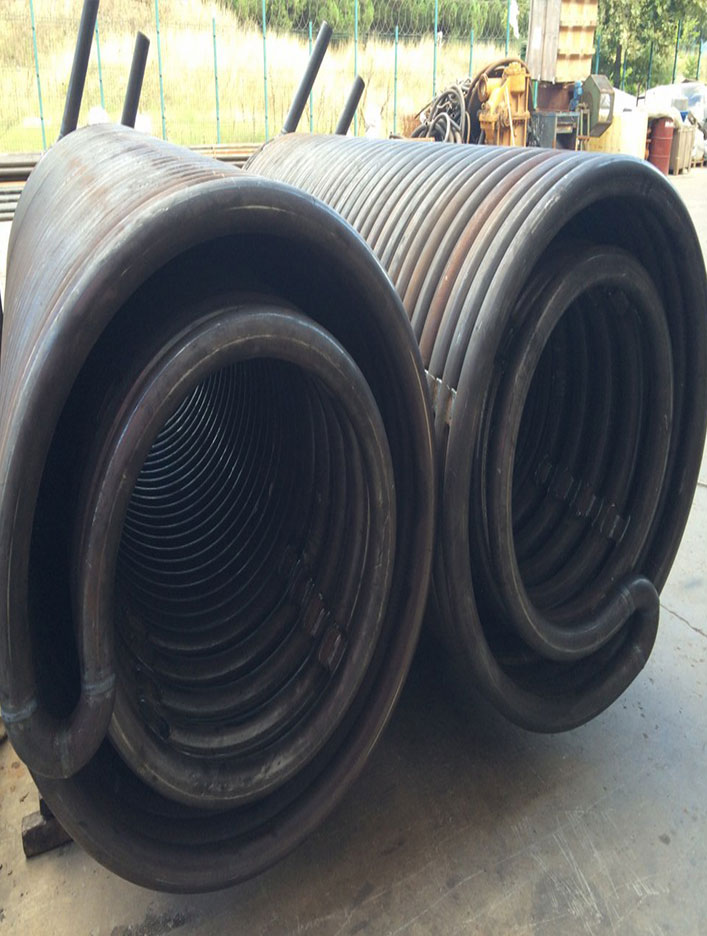
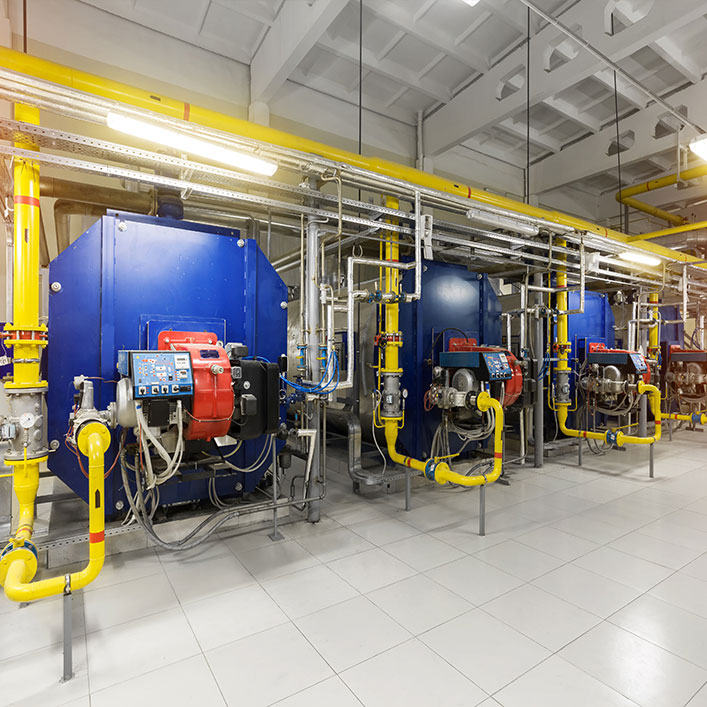
Advantages
High efficiencies
Which are 94% can be obtained with the
recuperator and up to 105% with the condensing economizer
according to the sensible heat for hot water generation.
Long life
is ensured by using machining methods in all
welded preparations and with World-class welding equipment
and welders.
Low Emissions
Are achieved thanks to the perfect
integration between the boiler and the burner.
Thermodynamic performance
Is achieved by calculation
with specially designed software and proven by site tests
Refractorless design
in the boiler because of well design
homogeneous heat flow.
Refractorless design
On burner and reversal chamber
eliminates the problems and increase the efficiency with
water-cooled chamber between the burner connection plate
and the furnace.

Have any Questions?
Call us Today!
+49 163 9702005
About Our Company
One of the most important aspects of certification is traceability. MNK has
established a traceability system according to the heat number, order and
certificate numbers for all materials used in the pressure parts as required by the
standards. MNK transfers permanent hard stamps on the materials and keep the
records for 10 years...
Download PDF