Supplementary Fired Waste Heat Boilers are used to increase cogeneration overall efficiency by burning additional fuel after the gas turbines.
Supplementary firing is an excellent way to generate additional steam in
cogeneration plants
Since the sensible heat recovered in the economizer in waste heat boilers is small compared to the heat of evaporation, most of the flue gas is thrown into the atmosphere without being used.
This waste heat is recovered in the economizer by increasing the evaporator capacity.
In addition, while 93% of the LHV value of the fuel is used in normal gas fired boilers, almost 100% is used in additional combustion boilers.
The oxygen required for additional post-combustion is provided by the oxygen in the exhaust of gas turbines operating with high excess air.
Since the sensible heat recovered in the economizer in waste heat boilers is small compared to the heat of evaporation, most of the flue gas is thrown into the atmosphere without being used.
This waste heat is recovered in the economizer by increasing the evaporator capacity.
In addition, while 93% of the LHV value of the fuel is used in normal gas fired boilers, almost 100% is used in additional combustion boilers.
The oxygen required for additional post-combustion is provided by the oxygen in the exhaust of gas turbines operating with high excess air.
Key Features
Steam | Efficiency | Capacity | Pressure | Steam Temperature | Gas Temperature |
---|---|---|---|---|---|
Saturated or Superheated | up to %100 ** | up to 35 t/h | up to 60 barg | up to 530°C | up to 1.000°C |
1) for 5 MWe Taurus 60, bigger turbines are available
**) based on sensible heat
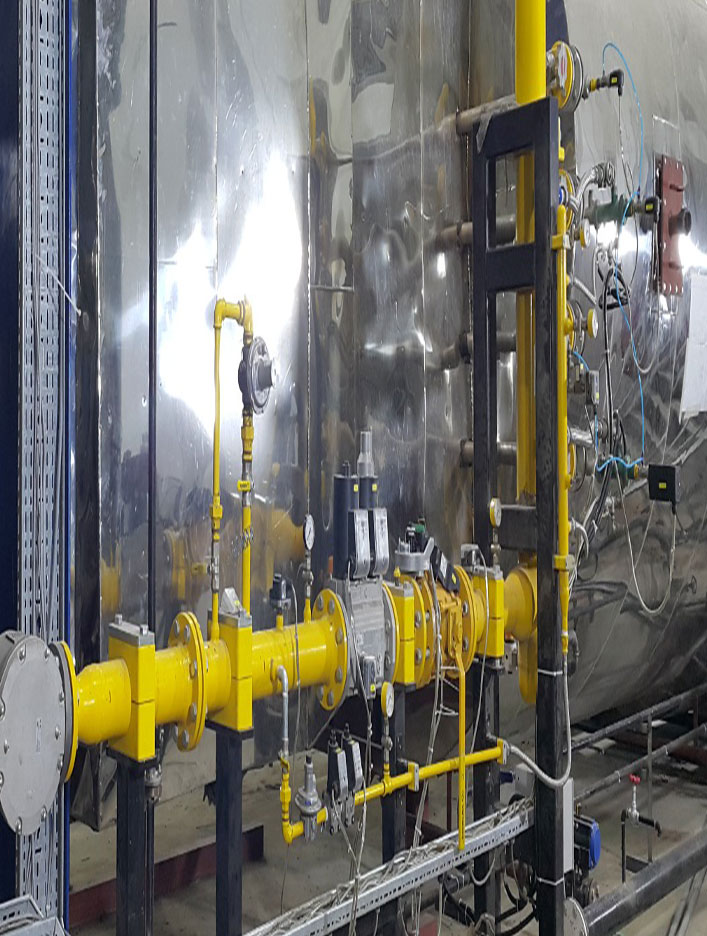
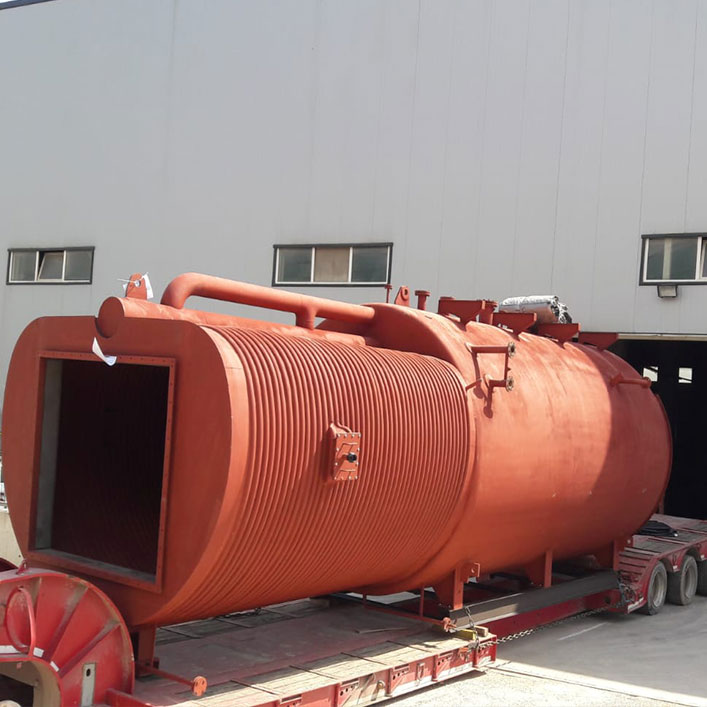
Advantages
High efficiencies
is achieved by choosing appropriate pinch
and approach points.
Long life
is ensured by using machining methods in all
welded preparations and with World-class welding equipment
and welders.
Thermodynamic performance
Is achieved by calculation
with specially designed software and proven by site tests
Fresh Air Fire
Steam generation operation is available when
the turbine is not operating.
High frequency welded spiral finned tubes
used for clean
gases makes compact design boiler.
Condensing economizer
Can recover very significant
amount of heat by cooling the flue gas

Have any Questions?
Call us Today!
+49 163 9702005
About Our Company
One of the most important aspects of certification is traceability. MNK has
established a traceability system according to the heat number, order and
certificate numbers for all materials used in the pressure parts as required by the
standards. MNK transfers permanent hard stamps on the materials and keep the
records for 10 years...
Download PDF